Mejorar la presentación de nuestros equipos
En el foro se comenta mucho sobre fabricarse esto o lo otro, pero y una vez que esta armado y funcionando ¿Dónde lo metemos? ¿Cómo lo metemos?
Esto que escribo no le va a solucionar la vida a nadie, pero tal vez se la simplifique un poco al momento de terminar el armado de algo.
Gabinetes en general:
Si el contenido del equipo no es pesado, se puede emplear este método:
Se compran (a medida) 6 chapas del material que se les ocurra (Aluminio o hierro)
2 Serán piso y tapa, 2 frente y fondo y las últimas serán los 2 laterales.
¿Y ahora que hago con todo esto?.
Seguimos comprando, un par de metros ángulo de aluminio con ala de unos 8 a 10mm y comenzamos a hermanar partes.
Comenzaremos con los laterales, sobre el borde de la chapa lateral fijamos un trozos de ángulo de aluminio mediante tornillos o remaches “POP” (Creo que en otros países les dicen remaches rápidos) con 2 o 3 tornillos o remaches por lado quedara bien (Tornillos de 3mm o 1/8´ o remaches de 3,5mm.
Continuamos con los otros 3 lados de la chapa lateral y luego pasamos al otro lateral y hacemos lo mismo.
Terminados los laterales, nos dedicamos al piso del futuro engendro.
En este tendremos que distribuir las partes componentes y prever las perforaciones pertinentes.
Lo mismo para el fondo del gabinete, pasa-cables, porta-fusibles, fichas de entrada y salida, todo lo que no se coloque en el frente ira en la parte posterior.
En este momento se supone tenemos el piso y el fondo perforado y los laterales rebordeados de ángulo de aluminio.
Buen momento para fijar los laterales al piso, para lo cual seguimos empleando o los tornillos o los remaches.
Si el frente y contrafrente llevan mucho cableado, será practico preparar las perforaciones pero no fijarlos con sus remaches o tornillos al resto del gabinete hasta luego de terminado su cableado.
No me olvide, la tapa se pondrá solo con tornillos y en ultimo lugar.
Frente con dibujos y todo:
El frente como es la parte mas visible debe ser en la que mas esmero habrá que poner
Para el frente existen 2 posibilidades, la sencilla que es frente simple y la más profesional que es frente doble.
La de frente simple sería de la siguiente forma
Piden prestado un programa de diseño que se llama Corel, aconsejo este porque es el que me gusta más, pero puede ser cualquier otro.
Con este programa se arman las plantillas de perforado del frente y contrafrente y el diseño de de la imagen del frente con graduación de potenciómetros, señalización de entradas, salidas, bueno, lo que se requiera.
Con la plantilla de perforado que se pegara a la chapa del frente, directamente se emplea para marcar y luego perforar con la o las mechas (Brocas) pertinentes.
Si por ejemplo se quiere colocar un display, se dibuja un rectángulo de tamaño inferior al necesario y sobre este trazado, se irán haciendo agujeros lo más cercanos posibles que luego se unirán entre si cortando el material entre estos con un corta-hierro o en caso de alta tecnología con una caladora.
El acabado final del agujero rectangular se dará con lima, sudor y lágrimas.
El frente más profesional es en realidad un doble frente (Habrá que fabricar 2 del mismo tipo.
El frente de montaje se prepara con el método descrito, y en este se montarán todas las partes a las que se tendrá acceso desde el exterior.
El frente de vista solo contendrá agujeros por los que pasarán ejes de potenciómetros, palancas de interruptores, Etc
Cuando me refiero a ejes quiero decir ejes, NO ROSCAS, estos agujeros son mucho menores que los de montaje (Montaje 12mm, eje 8mm)
Para no dejar tornillos visibles en el frente de “Vista”, se pueden agregar un par de “asas” y con los propios tornillos de fijación de estas se hermana frente y doble-frente de vista
El doble frente podrá ser del mismo tamaño que el frente de montaje o unos 25mm mas de ancho para cada lado, lo que servirá si se hizo todo con las medidas correctas para armar un Rack
La serigrafía del frente:
Esto es fácil, con el mismo programa de diseño arman el frente con colores, funciones, textos, todo lo que se les ocurra.
Se compran una hoja de “transfer”, la imprimen en inverso y la pasan al frente del equipo.
O se compran una hoja de auto-adhesivo para imprimir (Ambas se pueden imprimir a color con chorro de tinta) esta última se le saca la película protectora, y se adhiere al frente.
Siempre conviene darle una capa de barniz en aerosol para proteger los dibujos a largo plazo
La hojas de transferencia (Transfer) o de imprimir auto-adhesivo se compran en librerías que tengan material para profesionales (Muy normales cerca de universidades o facultades de arquitectura, diseño, Etc)
Equipos muy pesados:
En este caso el propio peso del o los transformadores deformaría el piso del gabinete.
La mejor solución que encontré es mandar a hacer a un herrero una especie de pecera de hierro ángulo (Claro que sin los vidrios), una especie de caja pero sin caras, solo estructura, las 2 caras laterales podrán ser de chapa común, la cara posterior puede servir para poner los disipadores y la frontal para el frente (Obvio) y el piso, bueno tendrá que ser un tanto mas grueso para soportar el peso del transformador.
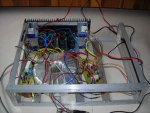
Del mismo bastidor (Con forma de pecera) se pueden sujetar unas bonitas “asas” que se compran en alguna casa de herrajes y dará un aspecto de “Comprado”
También es válido el doble frente y las orejas para Rack.
Algunos Tip´s de montaje.
Una fuente de escuadras de montaje ya roscadas y con sus correspondientes tornillos “Cabeza tanque” son las borneras para telefonía.
A los que no las conocen, son unas placas de bronce con 3 agujeros en línea roscados, y fijados con tornillo a un listón de baquelita.
Se retira de la base de baquelita, se retiran los tornillos y con 1 pinza y un pequeño martillo se escuadran a 90º, y lista la escuadra de montaje, uno de los agujeros servirá para fijar la PCB y el otro irá fijado al chasis.
Si se desea colocar la PCB horizontal, una fuente de separadores son las lapiceras bolígrafo, a estas se les retira el tubo con la tinta y luego se corta el plástico en trozos de la medida deseada.
Se arma un sandwitch con: Piso del gabinete, separador (Pedazo de bolígrafo), PCB, arandela y tuerca, todo atravesado por un tornillo, con un par de estos soportes cualquier placa quedará firme.
Existen comercialmente pilares para sostener plaquetas, pilares con traba en ambos extremos (Auto-anclaje), bujes roscados en ambos extremos también para montaje, que quedan muy bonitos pero hay que salir a comprarlos y no son fáciles de conseguir.
Cableados:
Si el largo de los cables no afecta el funcionamiento del circuito quedara mucho mas prolijo armar una manguera con todos los cables que vallan paralelos al frente de equipo, den vuelta en la esquina de gabinete y vallan hasta la placa siempre con dobleces a 90º.
Esta manguera se pueden zunchar con precintos plásticos, atar tipo matambre (Arrollado de carne) o conseguir un pedazo de cinta plástica helicoid (Es una cinta de cierto espesor que se enrosca por si sola como los cables espiralados de teléfono).
El método mas vistoso y que le gusta a Tiopepe123 es el atado, pero es bastante engorroso, por lo menos hasta tomar práctica.
A mi me gusta el de la cinta porque siempre olvido algún cable y tengo que desarmar todo y la cinta es recuperable.
Por ejemplo si están armando un pre-amplificador y quieren colocar a GND todas las entradas y salidas, un trozo de alambre de cobre de bobinar de buena sección pelado servirá para acoplar todas las tierras de las entradas y salidas.
A este mismo alambre se soldaran luego el neutro de la fuente de alimentación y la puesta a tierra del gabinete.
Esto evitará en muchos casos buscar luego zumbidos molestos.
Por ahora se acabo, si se me ocurre algo mas y tengo ganas de escribir lo agregare.
En el foro se comenta mucho sobre fabricarse esto o lo otro, pero y una vez que esta armado y funcionando ¿Dónde lo metemos? ¿Cómo lo metemos?
Esto que escribo no le va a solucionar la vida a nadie, pero tal vez se la simplifique un poco al momento de terminar el armado de algo.
Gabinetes en general:
Si el contenido del equipo no es pesado, se puede emplear este método:
Se compran (a medida) 6 chapas del material que se les ocurra (Aluminio o hierro)
2 Serán piso y tapa, 2 frente y fondo y las últimas serán los 2 laterales.
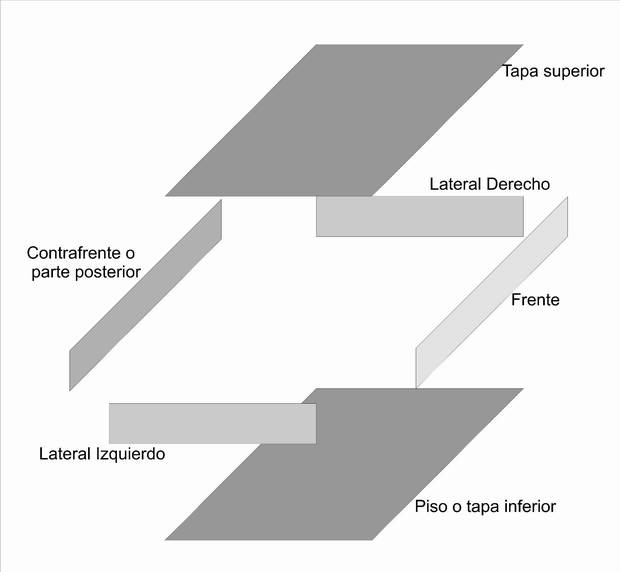
¿Y ahora que hago con todo esto?.
Seguimos comprando, un par de metros ángulo de aluminio con ala de unos 8 a 10mm y comenzamos a hermanar partes.
Comenzaremos con los laterales, sobre el borde de la chapa lateral fijamos un trozos de ángulo de aluminio mediante tornillos o remaches “POP” (Creo que en otros países les dicen remaches rápidos) con 2 o 3 tornillos o remaches por lado quedara bien (Tornillos de 3mm o 1/8´ o remaches de 3,5mm.
Continuamos con los otros 3 lados de la chapa lateral y luego pasamos al otro lateral y hacemos lo mismo.
Terminados los laterales, nos dedicamos al piso del futuro engendro.
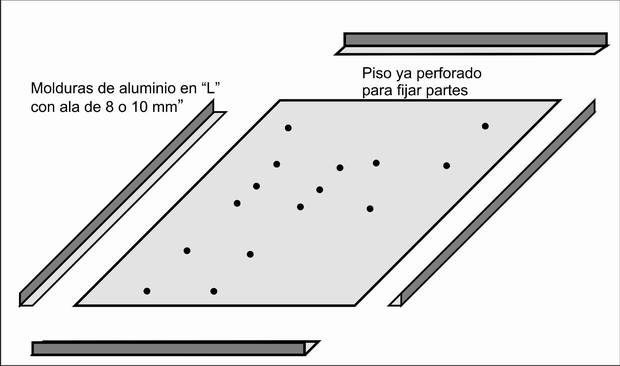
En este tendremos que distribuir las partes componentes y prever las perforaciones pertinentes.
Lo mismo para el fondo del gabinete, pasa-cables, porta-fusibles, fichas de entrada y salida, todo lo que no se coloque en el frente ira en la parte posterior.
En este momento se supone tenemos el piso y el fondo perforado y los laterales rebordeados de ángulo de aluminio.
Buen momento para fijar los laterales al piso, para lo cual seguimos empleando o los tornillos o los remaches.
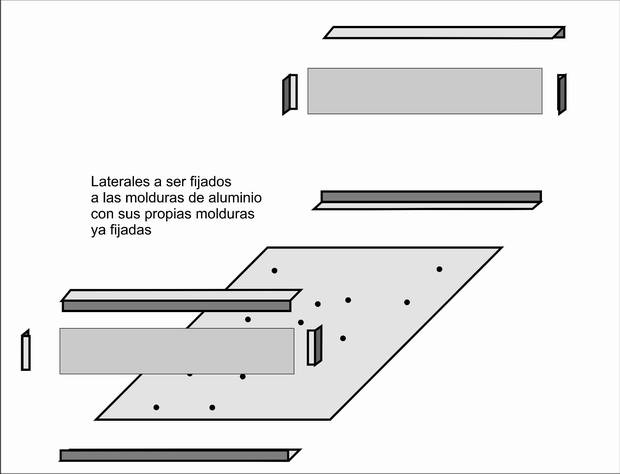
Si el frente y contrafrente llevan mucho cableado, será practico preparar las perforaciones pero no fijarlos con sus remaches o tornillos al resto del gabinete hasta luego de terminado su cableado.
No me olvide, la tapa se pondrá solo con tornillos y en ultimo lugar.
Frente con dibujos y todo:
El frente como es la parte mas visible debe ser en la que mas esmero habrá que poner
Para el frente existen 2 posibilidades, la sencilla que es frente simple y la más profesional que es frente doble.
La de frente simple sería de la siguiente forma
Piden prestado un programa de diseño que se llama Corel, aconsejo este porque es el que me gusta más, pero puede ser cualquier otro.
Con este programa se arman las plantillas de perforado del frente y contrafrente y el diseño de de la imagen del frente con graduación de potenciómetros, señalización de entradas, salidas, bueno, lo que se requiera.
Con la plantilla de perforado que se pegara a la chapa del frente, directamente se emplea para marcar y luego perforar con la o las mechas (Brocas) pertinentes.
Si por ejemplo se quiere colocar un display, se dibuja un rectángulo de tamaño inferior al necesario y sobre este trazado, se irán haciendo agujeros lo más cercanos posibles que luego se unirán entre si cortando el material entre estos con un corta-hierro o en caso de alta tecnología con una caladora.
El acabado final del agujero rectangular se dará con lima, sudor y lágrimas.
El frente más profesional es en realidad un doble frente (Habrá que fabricar 2 del mismo tipo.
El frente de montaje se prepara con el método descrito, y en este se montarán todas las partes a las que se tendrá acceso desde el exterior.
El frente de vista solo contendrá agujeros por los que pasarán ejes de potenciómetros, palancas de interruptores, Etc
Cuando me refiero a ejes quiero decir ejes, NO ROSCAS, estos agujeros son mucho menores que los de montaje (Montaje 12mm, eje 8mm)
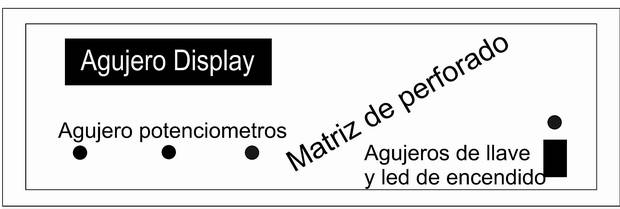
Para no dejar tornillos visibles en el frente de “Vista”, se pueden agregar un par de “asas” y con los propios tornillos de fijación de estas se hermana frente y doble-frente de vista
El doble frente podrá ser del mismo tamaño que el frente de montaje o unos 25mm mas de ancho para cada lado, lo que servirá si se hizo todo con las medidas correctas para armar un Rack
La serigrafía del frente:
Esto es fácil, con el mismo programa de diseño arman el frente con colores, funciones, textos, todo lo que se les ocurra.
Se compran una hoja de “transfer”, la imprimen en inverso y la pasan al frente del equipo.
O se compran una hoja de auto-adhesivo para imprimir (Ambas se pueden imprimir a color con chorro de tinta) esta última se le saca la película protectora, y se adhiere al frente.
Siempre conviene darle una capa de barniz en aerosol para proteger los dibujos a largo plazo
La hojas de transferencia (Transfer) o de imprimir auto-adhesivo se compran en librerías que tengan material para profesionales (Muy normales cerca de universidades o facultades de arquitectura, diseño, Etc)
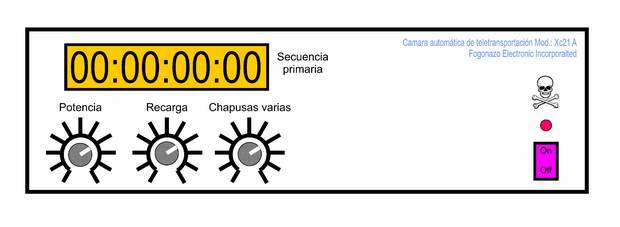
Equipos muy pesados:
En este caso el propio peso del o los transformadores deformaría el piso del gabinete.
La mejor solución que encontré es mandar a hacer a un herrero una especie de pecera de hierro ángulo (Claro que sin los vidrios), una especie de caja pero sin caras, solo estructura, las 2 caras laterales podrán ser de chapa común, la cara posterior puede servir para poner los disipadores y la frontal para el frente (Obvio) y el piso, bueno tendrá que ser un tanto mas grueso para soportar el peso del transformador.
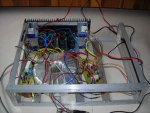
Del mismo bastidor (Con forma de pecera) se pueden sujetar unas bonitas “asas” que se compran en alguna casa de herrajes y dará un aspecto de “Comprado”
También es válido el doble frente y las orejas para Rack.
Algunos Tip´s de montaje.
Una fuente de escuadras de montaje ya roscadas y con sus correspondientes tornillos “Cabeza tanque” son las borneras para telefonía.
A los que no las conocen, son unas placas de bronce con 3 agujeros en línea roscados, y fijados con tornillo a un listón de baquelita.
Se retira de la base de baquelita, se retiran los tornillos y con 1 pinza y un pequeño martillo se escuadran a 90º, y lista la escuadra de montaje, uno de los agujeros servirá para fijar la PCB y el otro irá fijado al chasis.
Si se desea colocar la PCB horizontal, una fuente de separadores son las lapiceras bolígrafo, a estas se les retira el tubo con la tinta y luego se corta el plástico en trozos de la medida deseada.
Se arma un sandwitch con: Piso del gabinete, separador (Pedazo de bolígrafo), PCB, arandela y tuerca, todo atravesado por un tornillo, con un par de estos soportes cualquier placa quedará firme.
Existen comercialmente pilares para sostener plaquetas, pilares con traba en ambos extremos (Auto-anclaje), bujes roscados en ambos extremos también para montaje, que quedan muy bonitos pero hay que salir a comprarlos y no son fáciles de conseguir.
Cableados:
Si el largo de los cables no afecta el funcionamiento del circuito quedara mucho mas prolijo armar una manguera con todos los cables que vallan paralelos al frente de equipo, den vuelta en la esquina de gabinete y vallan hasta la placa siempre con dobleces a 90º.
Esta manguera se pueden zunchar con precintos plásticos, atar tipo matambre (Arrollado de carne) o conseguir un pedazo de cinta plástica helicoid (Es una cinta de cierto espesor que se enrosca por si sola como los cables espiralados de teléfono).
El método mas vistoso y que le gusta a Tiopepe123 es el atado, pero es bastante engorroso, por lo menos hasta tomar práctica.
A mi me gusta el de la cinta porque siempre olvido algún cable y tengo que desarmar todo y la cinta es recuperable.
Por ejemplo si están armando un pre-amplificador y quieren colocar a GND todas las entradas y salidas, un trozo de alambre de cobre de bobinar de buena sección pelado servirá para acoplar todas las tierras de las entradas y salidas.
A este mismo alambre se soldaran luego el neutro de la fuente de alimentación y la puesta a tierra del gabinete.
Esto evitará en muchos casos buscar luego zumbidos molestos.
Por ahora se acabo, si se me ocurre algo mas y tengo ganas de escribir lo agregare.
Última edición: