Bueno, un año después del ingreso al foro, he construido un soldador desde cero, con materiales reciclados.
Tengan paciencia si no sale todo desde el principio, subiré todas las fotos que pueda.
La lista de estos materiales es la siguiente:
01 Un segmento de planchuela (fleje) de 10mm ancho, por 3 mm de espesor, y 190 mm de largo. Este será el mango y apoyo de la punta y resistencia.
02 Una llave (sí, sí, una llave).
03 Alambre de nicrom, obtenido de la resistencia de un caloventor (60 cm. o lo que mida 5 ohms), más 2 cm de cada lado para la conexión..
04 Fibra de vidrio obtenida de cable telefónico.
05 Cinta aislante.
06 Cable para conectar a la alimentación de 2 por uno y medio (es lo que había).
07 Dos tornillos con su tuerca, arandela grower, y arandela (que si es con la forma de la que yo usé mejor , extraídos de ustedes ya saben)
08 Alambre de hierro común de 0,6mm de grosor, este será el intermedio entre el alambre de nicrom, y el cable de conexión( de ese modo, se evita que el cobre entre en contacto con el nicrom caliente, y se garantiza que el primero no se oxide y produzca falsos contactos).
09 Funda de fibra(espagueti), de la que se usa para aislar resistencia, recuperada de algún artículo electrónico (de 4 medidas distintas):
A para el alambre de 0,6mm
B para cubrir la conexión entre el cable y el alambre.
C para cubrir el conjunto resistencia y punta, y para la planchuela.(el mas grande)
10 Flux (unas gotas)
11 Talco (muy poco, ni medio gramo),sí aisla(eléctrica y térmicamente), se me ocurrió, porque en un tutorial de vitrofusión lo usaban para que no se pegara el vidrio al molde, entonces deduje que soportaría altas temperaturas
10 Un transformador toroidal de los que se usan para dicroica o uno electrónico(es indiferente).
Con el transformador debieran venir dos borneras dobles (entrada 220V, y salida 12V)
De lo contrario….
11 dos borneras dobles.
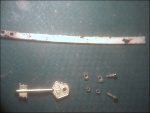
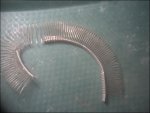
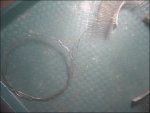
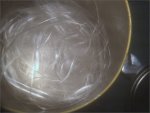
Herramientas:
Taladro y broca de 3mm.
Amoladora angular con disco flap (de lija) yo usé esto, pero de no haberla tenido, no me hubiera costado usar sierra y lima.
Lija. al agua (papel de lija 120 o 150).
Pinzas varias, alicate, y una pequeña llave ajustable.
Aquí no coloco imágenes porque no me parece necesario.
A trabajar.
01 Lo primero que haremos, son 2 perforaciones en un extremo de la planchuela, el primero a una distancia de 5 milímetros del extremo, el otro a 10 mm de este.(entiéndase, que cuando digo las distancias, me refiero al centro de cada orificio). En los materiales, ya se ve la planchuela con sus 2 orificios.
02 Luego atornillamos la llave en el orificio más alejado del extremo, usando el que ya tiene, (por donde se la coloca en el llavero), y ajustamos.
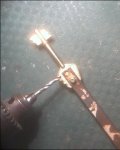
03 Con la llave atornillada, aprovechamos el segundo orificio de la planchuela, y perforamos un segundo orificio en la llave.
04 entonces colocamos un segundo tornillo y fijamos la llave en la planchuela.
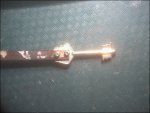
05 Ahora comienza la tarea de la sierra, la lima, o la amoladora.
A eliminamos un costado de la paleta.
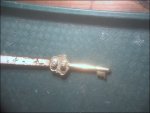
B eliminamos el otro[/B]
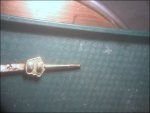
C rebajamos un costado de la cabeza de la llave, hasta quedar casi de la medida de la planchuela
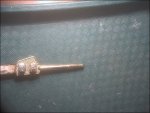
D rebajamos el otro.
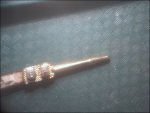
E le damos forma de punta al extremo donde estaba la paleta, y lijamos para que quede prolijo.
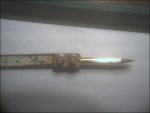
06 ahora viene la parte del “entalque”, mojamos el eje de la llave (la punta) a todo su largo (unos 4,5 cm)
Calentamos un poco para que se seque, y entalcamos, luego volvemos a mojar y repetimos la operación.
El resultado debiera ser algo así.
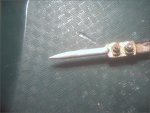
La idea de esto es obtener un aislante eléctrico barato, ¿lo importante?, funciona.
07 con la punta ya entalcada, procedemos a enrollar la resistencia. Desde la base y aprovechando los tornillos para trabar el alambre en las primeras vueltas.
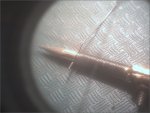
Cuando llegamos al extremo, dejamos 1 cm y para evitar que el alambre se afloje, lo atamos con un precinto de plástico,un trozo de cable o un remanente de resistencia, como en este caso.
08 ahora unimos a esa resistencia dos segmentos del alambre de hierro 0,6 de 10 cm de largo, y lo hacemos de modo que solo quede 1 mm de distancia al arrollado de resistencia.
09 colocamos funda de fibra a los dos alambres de hierro.(unos 3 cm)
10 procedemos a cubrir con una capa de fibra de vidrio todo el enrollado de resistencia, dejando libres los dos extremos de hierro, pero pasando del lado de la planchuela, 3 mm y del lado de la punta, algo más para dejar descubierto solo el sector que se usará para soldar.
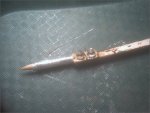
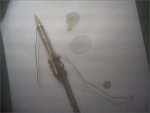
11 ahora, podemos acercar el alambre de hierro enfundado que quedó del lado de la punta, y unirlo al enrollado, cubriendo con una capa más de fibra de vidrio.
Y de ese modo quedarán ambos conectores cerca de los tornillos que unen llave y planchuela.
12 aflojamos ambos tornillos, y separamos llave y planchuela, para colocarle unas vueltas de fibra de vidrio, para aislar un poco el hierro de la planchuela, del bronce de la llave.
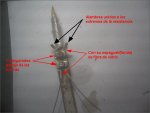
Por hoy basta de fotos, pero solo por hoy.
Tengan paciencia si no sale todo desde el principio, subiré todas las fotos que pueda.
La lista de estos materiales es la siguiente:
01 Un segmento de planchuela (fleje) de 10mm ancho, por 3 mm de espesor, y 190 mm de largo. Este será el mango y apoyo de la punta y resistencia.
02 Una llave (sí, sí, una llave).
03 Alambre de nicrom, obtenido de la resistencia de un caloventor (60 cm. o lo que mida 5 ohms), más 2 cm de cada lado para la conexión..
04 Fibra de vidrio obtenida de cable telefónico.
05 Cinta aislante.
06 Cable para conectar a la alimentación de 2 por uno y medio (es lo que había).
07 Dos tornillos con su tuerca, arandela grower, y arandela (que si es con la forma de la que yo usé mejor , extraídos de ustedes ya saben)
08 Alambre de hierro común de 0,6mm de grosor, este será el intermedio entre el alambre de nicrom, y el cable de conexión( de ese modo, se evita que el cobre entre en contacto con el nicrom caliente, y se garantiza que el primero no se oxide y produzca falsos contactos).
09 Funda de fibra(espagueti), de la que se usa para aislar resistencia, recuperada de algún artículo electrónico (de 4 medidas distintas):
A para el alambre de 0,6mm
B para cubrir la conexión entre el cable y el alambre.
C para cubrir el conjunto resistencia y punta, y para la planchuela.(el mas grande)
10 Flux (unas gotas)
11 Talco (muy poco, ni medio gramo),sí aisla(eléctrica y térmicamente), se me ocurrió, porque en un tutorial de vitrofusión lo usaban para que no se pegara el vidrio al molde, entonces deduje que soportaría altas temperaturas
10 Un transformador toroidal de los que se usan para dicroica o uno electrónico(es indiferente).
Con el transformador debieran venir dos borneras dobles (entrada 220V, y salida 12V)
De lo contrario….
11 dos borneras dobles.
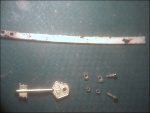
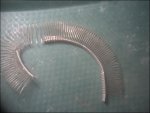
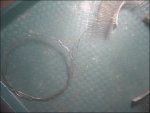
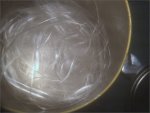
Herramientas:
Taladro y broca de 3mm.
Amoladora angular con disco flap (de lija) yo usé esto, pero de no haberla tenido, no me hubiera costado usar sierra y lima.
Lija. al agua (papel de lija 120 o 150).
Pinzas varias, alicate, y una pequeña llave ajustable.
Aquí no coloco imágenes porque no me parece necesario.
A trabajar.
01 Lo primero que haremos, son 2 perforaciones en un extremo de la planchuela, el primero a una distancia de 5 milímetros del extremo, el otro a 10 mm de este.(entiéndase, que cuando digo las distancias, me refiero al centro de cada orificio). En los materiales, ya se ve la planchuela con sus 2 orificios.
02 Luego atornillamos la llave en el orificio más alejado del extremo, usando el que ya tiene, (por donde se la coloca en el llavero), y ajustamos.
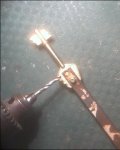
03 Con la llave atornillada, aprovechamos el segundo orificio de la planchuela, y perforamos un segundo orificio en la llave.
04 entonces colocamos un segundo tornillo y fijamos la llave en la planchuela.
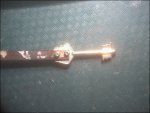
05 Ahora comienza la tarea de la sierra, la lima, o la amoladora.
A eliminamos un costado de la paleta.
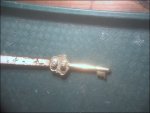
B eliminamos el otro[/B]
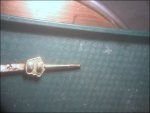
C rebajamos un costado de la cabeza de la llave, hasta quedar casi de la medida de la planchuela
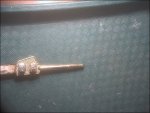
D rebajamos el otro.
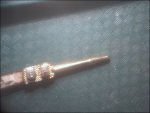
E le damos forma de punta al extremo donde estaba la paleta, y lijamos para que quede prolijo.
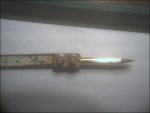
06 ahora viene la parte del “entalque”, mojamos el eje de la llave (la punta) a todo su largo (unos 4,5 cm)
Calentamos un poco para que se seque, y entalcamos, luego volvemos a mojar y repetimos la operación.
El resultado debiera ser algo así.
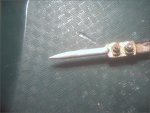
La idea de esto es obtener un aislante eléctrico barato, ¿lo importante?, funciona.
07 con la punta ya entalcada, procedemos a enrollar la resistencia. Desde la base y aprovechando los tornillos para trabar el alambre en las primeras vueltas.
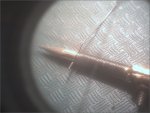
Cuando llegamos al extremo, dejamos 1 cm y para evitar que el alambre se afloje, lo atamos con un precinto de plástico,un trozo de cable o un remanente de resistencia, como en este caso.
08 ahora unimos a esa resistencia dos segmentos del alambre de hierro 0,6 de 10 cm de largo, y lo hacemos de modo que solo quede 1 mm de distancia al arrollado de resistencia.
09 colocamos funda de fibra a los dos alambres de hierro.(unos 3 cm)
10 procedemos a cubrir con una capa de fibra de vidrio todo el enrollado de resistencia, dejando libres los dos extremos de hierro, pero pasando del lado de la planchuela, 3 mm y del lado de la punta, algo más para dejar descubierto solo el sector que se usará para soldar.
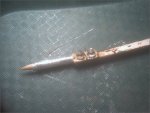
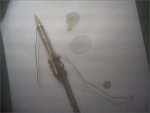
11 ahora, podemos acercar el alambre de hierro enfundado que quedó del lado de la punta, y unirlo al enrollado, cubriendo con una capa más de fibra de vidrio.
Y de ese modo quedarán ambos conectores cerca de los tornillos que unen llave y planchuela.
12 aflojamos ambos tornillos, y separamos llave y planchuela, para colocarle unas vueltas de fibra de vidrio, para aislar un poco el hierro de la planchuela, del bronce de la llave.
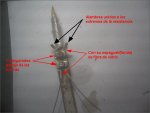
Por hoy basta de fotos, pero solo por hoy.
Última edición: