Hola a todos. Por motivos personales llevo mucho tiempo sin participar en el foro, pero ahora me gustaría mostraros mis últimos proyectos, que para evitar disparidades (y si los administradores no tienen inconveniente) englobaré en este único tema...
Comenzaré por el asunto en que estoy ahora, que es una serie de experiencias con semiconductores básicos como germanio, silicio, y otros cristales que comenzaron a usarse en los principios de la radio, como la galena, el carburo de silicio, la pirita, etc... y para ello me he hecho con un pequeño surtido de materiales que muestro a continuación:
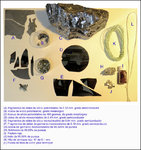
Como veis en la descripción se trata de germanio y de silicio de grado metalúrgico y semiconductor, y teniendo en cuenta que las experiencias absorben solamente un par de milímetros cuadrados cada vez, hay material para cientos de pruebas...
...El bloque de silicio de casi medio kilo me lo regaló un compañero de otro foro y procede de una fábrica de placas solares. En este caso ignoro sus características, pero lo más probable es que sea de un grado metalúrgico o superior, es de tipo policristalino, aunque es seguro que no debe alcanzar el grado de semiconductor del que se cortan finalmente las obleas. En el silicio lo más interesante son las obleas en sí, tanto la que es de una pieza como los trozos, ya que son directamente utilizables para experiencias de difusión.
...El germanio es también muy interesante, los fragmentos son policristalinos pero los trozos de oblea son monocristalinos y pueden ser dopados con relativa facilidad.
De elementos dopantes tengo por ahora unos 5 gramos de Indio, que crea impurezas de tipo P (formación de huecos), y de Fósforo y Antimonio, ambos de tipo N (aportación de electrones). También estoy esperando unos 20 gramos de Galio, que como el Indio y el Aluminio, es de tipo P.
La difusión de dopantes se ha de efectuar en un horno eléctrico, a temperaturas que rondan los 500 Cº para el germanio y más de 800 para el silicio, y en atmósfera de gas inerte. Entonces, para medir la temperatura es necesario utilizar termopares, para esto construiré termopares extremadamente delgados de tipo "K", utilizando hilos de cromo y alumel, de tan sólo 0,1 mm de diámetro. Y para proteger los hilos utilizaré además funda de fibra de vidrio.
En realidad ya he hecho algunas cosas con estos materiales, en próximos mensajes lo iré mostrando...
Un saludo a todos
Comenzaré por el asunto en que estoy ahora, que es una serie de experiencias con semiconductores básicos como germanio, silicio, y otros cristales que comenzaron a usarse en los principios de la radio, como la galena, el carburo de silicio, la pirita, etc... y para ello me he hecho con un pequeño surtido de materiales que muestro a continuación:
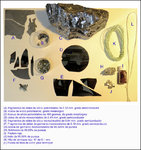
Como veis en la descripción se trata de germanio y de silicio de grado metalúrgico y semiconductor, y teniendo en cuenta que las experiencias absorben solamente un par de milímetros cuadrados cada vez, hay material para cientos de pruebas...
...El bloque de silicio de casi medio kilo me lo regaló un compañero de otro foro y procede de una fábrica de placas solares. En este caso ignoro sus características, pero lo más probable es que sea de un grado metalúrgico o superior, es de tipo policristalino, aunque es seguro que no debe alcanzar el grado de semiconductor del que se cortan finalmente las obleas. En el silicio lo más interesante son las obleas en sí, tanto la que es de una pieza como los trozos, ya que son directamente utilizables para experiencias de difusión.
...El germanio es también muy interesante, los fragmentos son policristalinos pero los trozos de oblea son monocristalinos y pueden ser dopados con relativa facilidad.
De elementos dopantes tengo por ahora unos 5 gramos de Indio, que crea impurezas de tipo P (formación de huecos), y de Fósforo y Antimonio, ambos de tipo N (aportación de electrones). También estoy esperando unos 20 gramos de Galio, que como el Indio y el Aluminio, es de tipo P.
La difusión de dopantes se ha de efectuar en un horno eléctrico, a temperaturas que rondan los 500 Cº para el germanio y más de 800 para el silicio, y en atmósfera de gas inerte. Entonces, para medir la temperatura es necesario utilizar termopares, para esto construiré termopares extremadamente delgados de tipo "K", utilizando hilos de cromo y alumel, de tan sólo 0,1 mm de diámetro. Y para proteger los hilos utilizaré además funda de fibra de vidrio.
En realidad ya he hecho algunas cosas con estos materiales, en próximos mensajes lo iré mostrando...
Un saludo a todos