Bueno...vamos a comenzar a medir sobre el engendro que hemos armado, pero antes de empezar con eso hay que poner otro pequeño disipador que enlace los dos drivers + el multiplicador Vbe que son: Q3, Q4 y Q5. TENES QUE PONERLO!!!! No empecés a medir sin este disipador montado por que el multiplicador Vbe debe sensar la temperatura de los drivers, así que deben estar todos juntos!!!
Yo usé un par de recortes de un disipador de fuente de PC (viste como estamos aprovechando los cachivaches esos?), y lo hice por que ya trae los tornillos y el metal roscado para sujetarlos, así que con solo cortar dos franjas de un disipador de esos estamos hechos con nuestra necesidad. Queda mas o menos así:
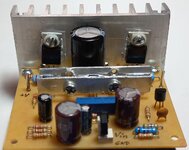
Podría haber quedado mas bonito...pero bué, lo mismo es funcional. Fijate como se usan los tornillos y la rosca que ya trae el disipador y solo hay que hacer dos perforaciones ALINEADAS con los huecos en el otro recorte de aluminio para que pasen los tornillos y puedan apretar "el sandwich" de transistores.
Ahora sí vamos a comenzar a ajustar la polarización estática, pero primero tenes que conseguirte un destornillador pequeño que permita girar el tornillo del trimpot sin hacer cortocircuito con lo que hay cerca. Yo tengo esos que vienen aislados, pero los compré hace como 40 años y no sé si ahora existen los mismos, pero hay algunos parecidos:
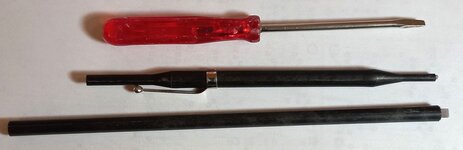
Ahí también hay uno de los comunes, pero no está aislado por que lo uso para otras cosas. Si no tenés dinero para comprar uno aislado no pasa nada: te conseguís uno como el de mango rojo (por acá les llaman "perilleros") y le aislás el vástago con un poco de termocontraíble. Con eso solucionás el problema y evitás quemar componentes si se te escapa el destornillador mientras ajustás el trimpot por que no me quedó del todo cómodo.
MUY IMPORTANTE!!!: Antes de empezar a ajustar nada, y con el PCB completamente desconectado de todo, vas a girar el tornillo del trimpot hacia la izquierda, dándole todas las vueltas que sean necesarias para mandar el cursor al fondo. Si querés asegurarte que llegó, podés medir resistencia (por el lado del cobre del PCB) entre el terminal central del trimpot y el terminal que está cerca de C3, y te debe dar 0 ohms si el cursor está al final.
Es muy importante que hagás esto por que si nó podés volar a la mie@#$%& los transistores de salida.
Ahora comienzan los problemas, por que yo tengo una fuente de "laboratorio" (ponele) que construí hace mas de 30 años y funciona OK para lo que vamos a hacer. Si vos no tenés una fuente similar entonces vas a tener que esperar hasta que diseñemos la fuente de este amplificador para que puedas probar con ella directamente. De todas formas, vamos a explicar el proceso de ajuste y los problemas que yo tuve:
Primero tenés que conectar la alimentación del amplificador a los terminales gordos que se llaman
GND y
Vcc. Mirá el esquema que está abajo:
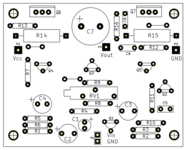
En
GND ponés la masa y en
Vcc ponés el positivo de la fuente de 34V (se usa esa tensión para conseguir los 15W). NO VAYAS A PONER LOS CABLES AL REVÉS POR QUE VAS A HACER UN DESASTRE!!!
Luego ajustás el tester a la escala de 200mV y ponés la punta POSITIVA en el extremo externo de la resistencia R14 (el que está sobre
Vcc) y la punta negativa en el extremo externo de la resistencia R15 (el que está sobre
GND). Más facil...imposible! Te vá a quedar algo mas o menos así:
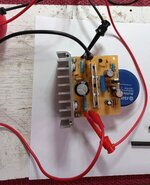
Los clips cocodrilo son de la fuente de alimentación y los cosos esos con ganchito en las resistencias son del tester, OK?
Si estás despierto y leyendo con atención, habrás advertido que los transistores Q2 y Q3 tienen la posición invertida entre el esquema del layout y el PCB de la foto de arriba. Eso es por que soy un salame y me equivoqué al diseñar el footprint de esos transistores en el KiCad. Yo lo arreglé a lo bruto pero ustedes van a recibir un PCB con el diseño correcto

. Fijate como quedó mi parche: solo dí vuelta los transistores y crucé la pata de Base para el otro lado...y problema resuelto:
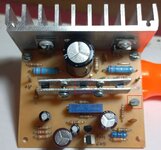
Con esto ya listo podemos empezar con el ajuste, que es bastaaaante simple:
Encendés la fuente de alimentación (siempre con una lámpara conectada en serie!!! Leé el
thread de
@Fogonazo por que vas a aprender un montón y vas a minimizar la quemazón de cosas), mirás cuanto marca el tester (acordate que debe estar en la escala de 200mV): si todo vá bien deberías leer algo de 0.1mV o 0.2mV, pero si se escapa de ese valor..
APAGÁ LA FUENTE DE ALIMENTACIÓN YAAAAAA!!!!! y vamos a tener que ver que sucedió.
Hacer el ajuste de la polarización estática es bien fácil: con todo conectado tal como vamos empezás a girar el tornillo del trimpot
hacia la derecha, pero lo hacés despacio y SIN APURARTE!!! Probablemente vas a darle varias vueltas y no vas a ver cambio de la lectura del tester, pero seguí girando SIN APURARTE y cuando el trimpot esté cerca del 35% del extremo frente a vos (estoy suponiendo que estás mirando el trimpot de frente...del lado del tornillo, OK?) vas a ver que comienza a aumentar la lectura del tester. CALMA!!! todo está OK y tenés que seguir girando a la derecha hasta que el tester te marque entre 13.2mV y 13.6mV, y eso equivale a un "BIAS" de 30mA en los transistores de salida (como se sabe? Fácil, aplicás la Ley de Ohm y te dá 13.2mV / 0.44ohm --> 30mA). Algo mas o menos así:
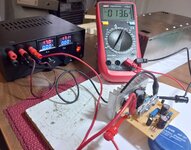
Cuando llegás a ese valor vas a parar de girar el trimpot y vas a dejar todo conectado y funcionando durante un rato...tipo 20 a 30 minutos y TE QUEDAS MIRANDO EL TESTER!!!! Vas a ver que a medida que pasa el tiempo la lectura de los 13.2mV comienza a variar y aumenta. Eso es normal, pero si el pequeño disipador está bien colocado
debería estabilizarse cerca de 15 a 17mV. No pasa nada, mientras que se estabilice y si queda quieta en algún momento estará todo OK.
Cuando pasó media hora volvés a retocar el ajuste del trimpot, pero ahora hacia la izquierda, cosa de bajar la tensión otra vez a los 13.2mV, y seguís con todo encendido durante otros 20 minutos MIRANDO EL TESTER!!! Ahora ya casi que no debería variar la lectura..tal vez 0.1 o 0.2mV está OK, y si ves que varía un poco más...repetís el proceso hasta que ya no cambie.
Antes de tirar fuegos artificiales, vamos a revisar como quedó el punto de operación del amplificador, y para eso ajustás el tester para medir 20V, colocás la punta negativa en el terminal
GND y la punta positiva EN EL OTRO TERMINAL de R14 o R15 (no en el mismo terminal donde mediste el bias, EN EL OTRO!!!): la lectura debe dar entre 16.5V y 16.8V...mV mas o mV menos (en el simulador me daba 16.69V y cuando medí me salió 16.76V... al lado, eh?)
Si llegamos hasta acá sin problemas, has ajustado la polarización estática de tu amplificador y te podés tomas unas buenas birras en su honor, pero antes vas y le pedís el esmalte de uñas a tu novia, tu mamá o tu hermana y pintás un poquito el tornillo del trimpot cubriendo también el frente del mismo...PERO LE PONES POCO!!!! Solo queremos evitar que se gire y no presentar una pintura abstracta en el
Museo de Arte Moderno.
Si llegaste hasta acá, estás muy bien encaminado y podés comenzar a repetir todo lo que hiciste hasta ahora para montar el segundo PCB de este amplificador estéreo...que es exactamente idéntico y se trabaja exactamente de la misma forma.
Yo voy a seguir con otras mediciones, ahora con osciloscopio y generador de señales, para verificar algunos resultados de la simulación y eventualmente hacer una revisión del PCB si encontrara algún problema, pero vos no vas a tener que hacerlas. Claro que no voy a publicar el PCB hasta que complete ese paso.
Continuará....